What is Poultry Ventilation System?
Ventilation is a management tool that allows poultry farmers to easily control air quality to optimize bird performance, health, and welfare. Poultry ventilation requirements change with growth and weather conditions. These requirements include aspects such as the amount of fresh air in cold weather or during brooding, to creating high airflow velocities to keep birds comfortable in hot or humid conditions.
Among these factors, humidity is the biggest challenge for poultry farmers, as it leads to wet litter and increased ammonia levels. These issues negatively impact the health, performance, and profitability of the broiler flock. Air exchange through poultry house ventilation is the only solution to the problem of excessive humidity. Poultry ventilation helps to exhaust moist indoor air and replace it with fresh outdoor air.
Inlet Window: What is a Poultry House Inlet?
An inlet window, also known as an air inlet or ventilation window in Persian, is a specialized type of window primarily used in poultry houses and sometimes in other industrial or agricultural environments to control and regulate the inflow of air into the building. These windows typically have manual or automatic adjustment mechanisms to control the amount and direction of incoming air. The inlet is effectively a window that controls the rate of air entering and exiting the poultry house, leading to reduced energy loss and increased efficiency.
Main Applications of Poultry House Fans (Air Exchangers):
- Fresh Air Supply: By extracting polluted air and replacing it with fresh outdoor air, fans maintain oxygen levels inside the building.
- Temperature Control: In warm seasons, fans create airflow to help cool the environment and prevent heat stress in poultry. In cold seasons, proper ventilation and preventing the accumulation of warm air at the ceiling help to distribute temperature evenly.
- Humidity Control: Fans remove moist air, preventing excessive humidity in the building, which can be a cause of diseases.
- Harmful Gas Reduction: The accumulation of gases like ammonia from poultry manure can be harmful to their health. Fans expel these gases from the building.
- Air Circulation: Creating proper airflow throughout the building helps to distribute temperature, humidity, and air quality evenly.
Common Types of Poultry House Fans (Air Exchangers):
- Wall Fans: These types of fans are usually installed on the side or end walls of the building and are used for exhausting air outwards.
- Roof Fans: These fans are installed on the roof of the building and can be used for exhausting air or in tunnel ventilation systems to create horizontal airflow.
- Circulation Fans: These fans are used to create airflow within the building and distribute temperature and humidity evenly. They are usually installed on the ceiling or suspended.
Important Features of Poultry House Fans (Air Exchangers):
- High Airflow Capacity (CFM/CMM): The ability to move a large volume of air per unit of time.
- High-Efficiency Motors: To reduce energy consumption and operating costs.
- Resistance to Environmental Conditions: Designed to operate in humid, corrosive, and dusty environments.
- High Durability and Lifespan: Due to continuous operation, they should be made of high-quality materials.
- Easy Maintenance: Simple design for ease of cleaning and servicing.
- Safety: Equipped with guards to prevent contact with the blades.
What are Fans and Air Exchangers?
A poultry fan (also known as a poultry house fan or air exchanger) is a mechanical device used for air circulation and ventilation inside poultry houses. The primary function of these fans is to extract polluted, hot, humid air containing harmful gases from inside the building to the outside, consequently facilitating the entry of fresh air through air inlets. This process plays a vital role in maintaining the health and comfort of the poultry, as well as production efficiency.
Main Applications of Poultry House Fans (Air Exchangers):
- Polluted Air Exhaust and Fresh Air Supply: By expelling polluted air containing moisture, harmful gases (such as ammonia), and particulate matter, fans allow fresh, oxygen-rich air to enter the building.
- Temperature Control: In warm seasons, fans help cool the environment by removing hot air and creating airflow. In cold seasons, proper ventilation and expelling the warm, humid air accumulated at the ceiling help to distribute temperature evenly (although in this case, adjusting fan speed and ventilation rate is important).
- Humidity Control: Fans prevent excessive humidity buildup in the building by removing moist air.
- Harmful Gas Reduction: Fans effectively remove harmful gases produced by poultry manure from the building.
- Air Circulation (Secondary Role of Some Fans): Some circulation fans are primarily used to create airflow within the building and distribute environmental conditions evenly, but the main task of air exhaust falls to wall and roof fans.
The Key Difference Between Poultry House Fans and Inlets
In poultry house ventilation systems, inlets (air inlet windows) and fans (air exchangers) are two fundamental components that play complementary roles in providing healthy air and regulating environmental conditions inside the building. Although both are involved in the ventilation process, their function and tasks are quite different. To better understand this difference, consider the following points:
Function:
- Fan (Poultry Fan/Air Exchanger): This is an active device that uses a motor and blades to forcefully draw air from inside the building to the outside. This action creates negative pressure inside the poultry house.
- Inlet (Inlet Window/Air Inlet): This is a passive device that allows fresh air from outside to enter the building due to the negative pressure created by the fans. Its operation depends on the functioning of the fans.
Main Task:
- Fan (Poultry Fan/Air Exchanger): The primary task is to exhaust polluted, hot, humid air containing harmful gases from inside the building to the outside.
- Inlet (Inlet Window/Air Inlet): The primary task is to supply fresh air and regulate the incoming airflow into the building. This includes controlling the amount of air and its direction for even distribution throughout the poultry house.
The Importance of Ventilation Systems in Poultry Farming
for the poultry. This is essential as birds need air with sufficient oxygen and minimal levels of carbon dioxide, carbon monoxide, ammonia, and dust. Inadequate ventilation leads to increased ammonia, carbon dioxide, and humidity, which in turn increases the occurrence of related syndromes such as ascites in poultry. Furthermore, high levels of ammonia in the flock can cause footpad dermatitis, eye burns, breast blisters, skin irritation, weight loss, poor uniformity, increased susceptibility to diseases, and blindness. The Cobb Broiler Management Guide provides the following table as a guideline for air quality in poultry farms:
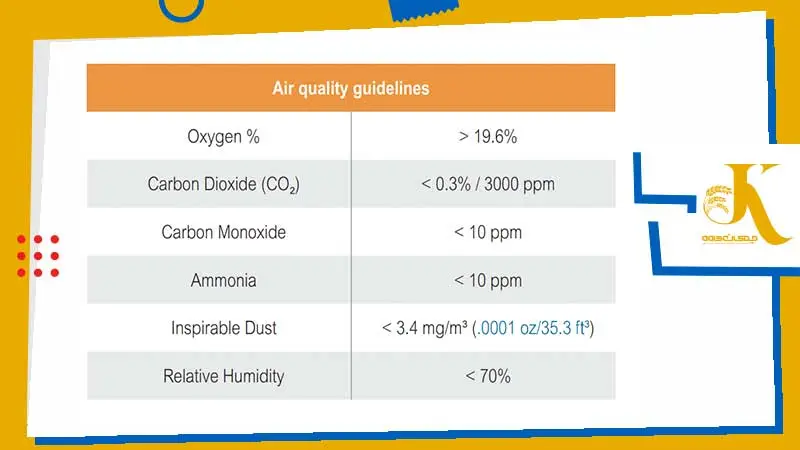
In every poultry house, ventilation systems are used to maintain optimal air quality. Ventilation systems are broadly categorized into two types: natural and mechanical. Natural ventilation refers to utilizing free-flowing air through windows. On the other hand, mechanical ventilation systems involve the use of poultry fans (air exchangers) and other mechanical ventilation units.
Natural Ventilation Systems in Poultry Houses – Design and Placement of Poultry House Windows
In natural ventilation systems, natural forces such as wind are responsible for air movement. This system typically utilizes windows to supply fresh air and exhaust carbon dioxide in poultry houses. The number and size of the windows should be appropriate for the poultry house and chick brooding. To improve ventilation quality, south-facing windows are usually placed near the floor (one meter from the floor), and north-facing windows are placed near the ceiling (at a half-meter distance). It’s also essential that the ratio of the air inlet surface area to the outlet area is less than 2 to 1 in this setup.
While this method involves lower energy consumption and costs, it’s not very practical today due to its disadvantages. There’s a high probability of insects and pests entering the poultry house. Consequently, it’s recommended to use netting for the windows. Additionally, due to the presence of windows, proper light control within the building is not achieved, necessitating darkening the windows. Moreover, during cold or hot seasons, this type of ventilation is insufficient for the poultry house environment.
For all the reasons mentioned, it’s recommended to use a mechanical ventilation system with cooling devices for better and easier control of airflow and temperature in poultry farming.
Mechanical Ventilation Systems
In newer industrial poultry farms, mechanical ventilation systems, meaning poultry fans (air exchangers) and artificial ventilation, are utilized. This system introduces fresh air into the poultry house and exhausts polluted air. Mechanical ventilation systems exist in two forms: positive pressure and negative pressure.
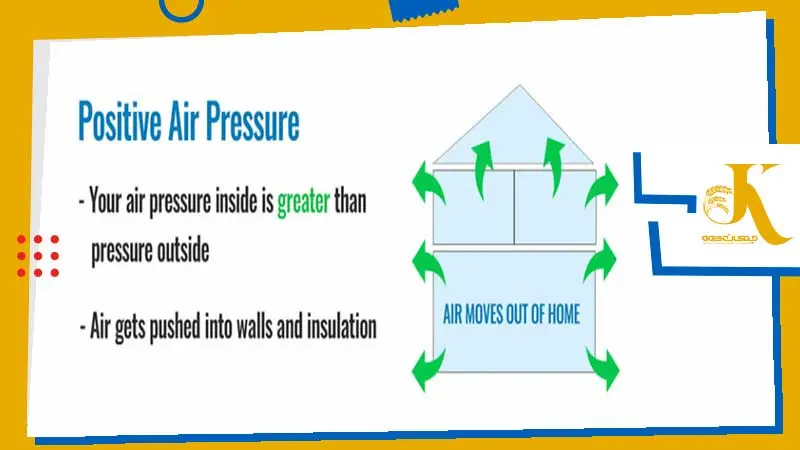
Positive Pressure Ventilation (Blower Ventilation)
Positive pressure ventilation involves forcing fresh air from the outside into the poultry house using a fan to create positive pressure, subsequently expelling stale air through an outlet on the opposite side. Essentially, in positive pressure ventilation, the fan draws clean, fresh outside air inwards. This method is generally employed in winter due to the use of heaters; otherwise, positive pressure ventilation fans are not typically used.
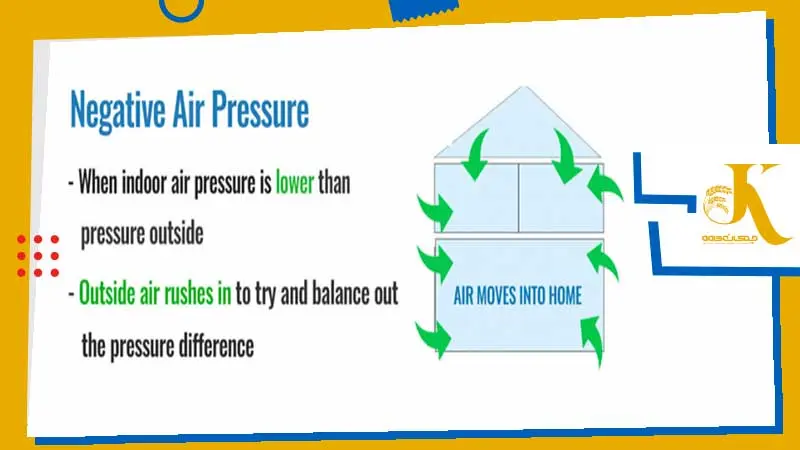
Negative Pressure Ventilation (Exhaust Ventilation)
Negative pressure ventilation means fresh air flows in through the air inlets, passes through the poultry house, and polluted air is exhausted by fans. Essentially, the principle of this ventilation is that when the exhaust fans are turned on, the air pressure inside the poultry house becomes slightly lower than the outside. This means the fans expel the stale air from the poultry house. In fact, designing the installation position of the negative pressure exhaust fan requires the volume of exhaust air to be slightly greater than the volume of incoming air. This ensures that the air pressure inside the poultry house is slightly lower than the outside, so fresh air from outside the building automatically flows in under the influence of the negative pressure. This type of ventilation is commonly used in all modern current poultry farms for raising chickens. There are various cooling methods for farms using negative pressure ventilation, including cross ventilation, tunnel ventilation, and transverse ventilation.
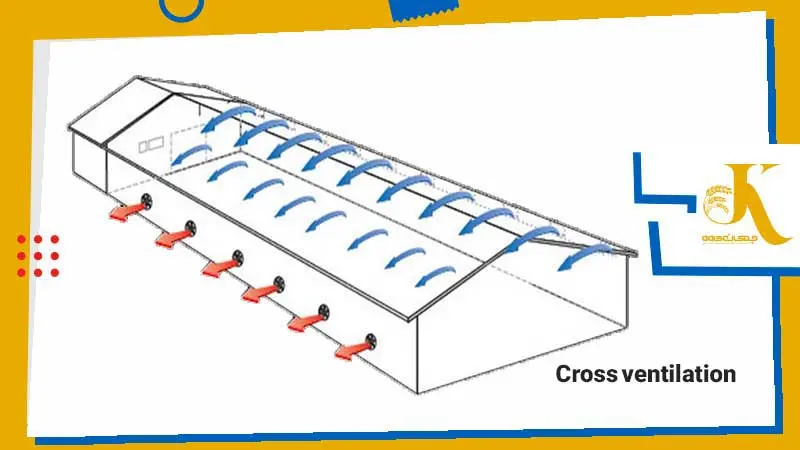
Poultry House Cross Ventilation
Cross ventilation in poultry houses involves installing exhaust fans on one side of the building and inlets (negative pressure air inlets) on the opposite side, across the width of the house.The adjustable inlet windows ensure a uniform temperature inside the poultry house.
This type of ventilation is designed in both positive and negative pressure systems. Despite its capabilities such as temperature regulation, improved air distribution, and reduced air entry points in the poultry house, it is rarely used in practice due to its drawbacks. The disadvantages of cross ventilation systems include:
- High equipment costs
- Installation of a large number of equipment units
- Difficult installation
- Limited range
Cross ventilation is typically used when the poultry house has a short length and a width of less than 10 meters. In a cross-ventilation system, fresh air enters through the inlets, passes completely through the poultry house, and is finally exhausted.
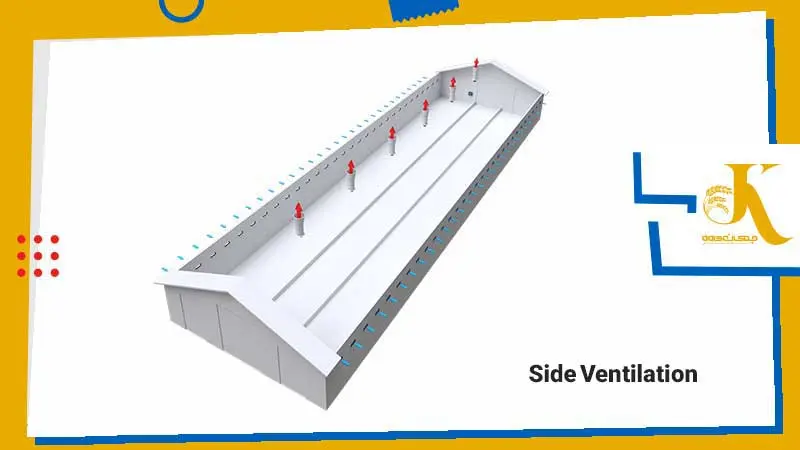
Poultry House Side Ventilation
Side ventilation is a system that ventilates the air in a poultry house and exhausts it through small inlets in the sidewall. . Side ventilation systems are suitable for most poultry farms with temperate climates. The goal of using side ventilation is to maintain temperature while providing fresh air in the poultry house. In essence, side ventilation is a negative pressure system that precisely regulates temperature, controls humidity, and manages airflow velocity.
In a side ventilation system, the walls, ceiling, or roof inlets create fresh air entry points. Side ventilation for broiler chickens is typically used from the third week onwards during spring or autumn. When the weather is warm, air enters the poultry house and is drawn out more quickly, resulting in air circulation around the chicks and cooling them. However, during cold weather, fresh air mixes with the air inside the poultry house before reaching the chicks. The method for calculating the number of side ventilation fans is as follows:
Number of Side Fans = Fan Ventilation Capacity / Minimum Ventilation Rate at Maximum Flock Weight
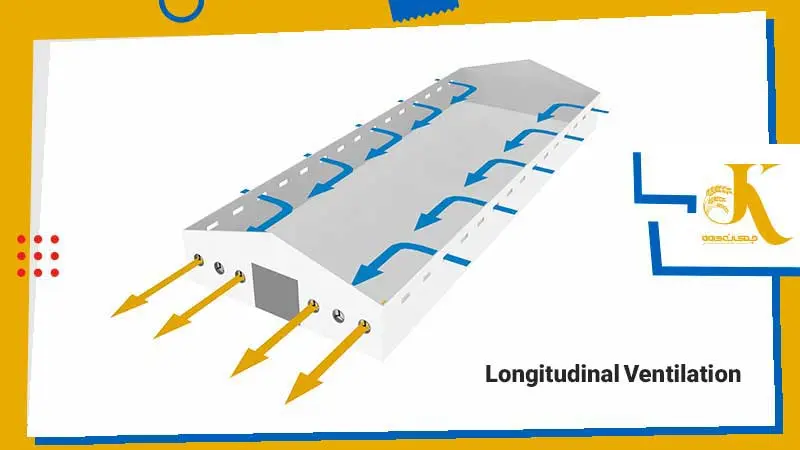
Poultry House Longitudinal Ventilation (Tunnel Ventilation)
Longitudinal ventilation involves using fans on one end wall and inlets on the sidewalls of the poultry house. This allows fresh air to pass through the longitudinal axis of the building and be exhausted under negative pressure. It can also be described as having negative pressure fans installed on one wall of the poultry house, with air inlets adjustable on any of the other three walls. This method not only has an optimized design but also reduces installation costs. This ventilation system is typically used in summer with high temperatures and humidity, and when the negative pressure in the poultry house is greater than 20-30 Pascals. In summer, evaporative cooling pads are usually installed at the air inlets to effectively cool the poultry house environment (i.e., evaporative cooling).
Furthermore, in rearing buildings longer than 80 meters and wider than 10 meters, a tunnel ventilation system, which is a type of longitudinal ventilation, is used. In this type of ventilation, the airflow in the longitudinal direction provides better cooling for the birds. Longitudinal ventilation is generally used during warm seasons or in hot weather. By increasing the airflow velocity in the poultry house, the longitudinal ventilation system cools the air and reduces the body temperature of the flock. In this method, a wide range of air exchange is possible by opening or closing air inlets and increasing or decreasing the speed of the fans. The following method is used to calculate the number of longitudinal fans in a poultry house:
Ventilation Volume = Airflow Velocity × Poultry House Cross-sectional Area / Fan Ventilation Volume
Poultry House= Poultry House Cross-sectional Area (m²) /Total Fan Capacity (m³/s)
In the modern poultry farming industry, the role of fans is crucial and undeniable. Therefore, calculating the number of ventilation fans, their position, and installation method is very important. Additionally, having a greater number of fans as backups in poultry houses is essential, as fans may break down or fail for various reasons. Finally, due to regional differences in summer temperature and humidity, and consequently wind speed, the optimal air velocity is usually considered to be 2.5 meters per second. The benefits of longitudinal ventilation systems in rearing buildings include:
- Optimized design
- Simple installation
- Low cost
- Good ventilation
- Cooling effect
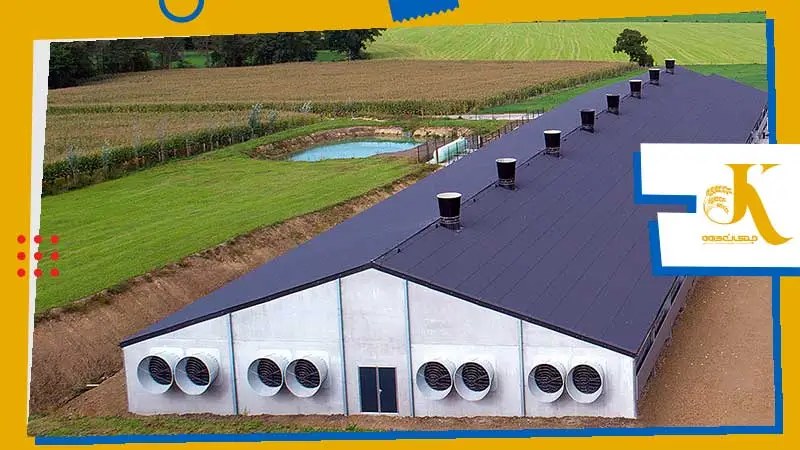
Ventilation Design Principles: Fan Types Based on Placement
The design of a ventilation system can vary depending on the climate. Sometimes poultry farmers think setting up ventilation is a very simple task – that you only need one or two fans turned on with a timer and the inlets opened for fresh air. However, this is not the case and it’s a very complex process. In Iran, we typically experience four seasons in most parts of the country. For this reason, three ventilation modes – minimum ventilation, transitional ventilation, and tunnel ventilation – are commonly used in designing poultry house ventilation systems.
Generally, in most countries and climates around the world, these three ventilation modes are essential for having the best chance of maintaining bird comfort. In the following sections, we will examine these three fan placement methods and the calculation of the number of poultry house fans needed.
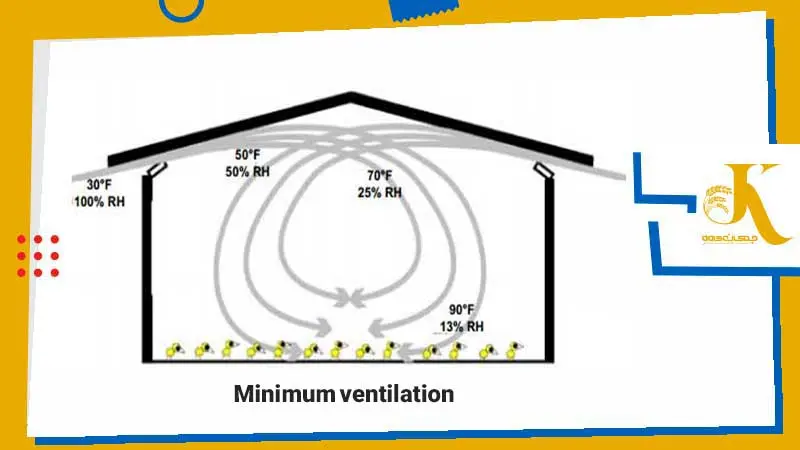
Poultry House Minimum Ventilation
Minimum ventilation refers to the minimum amount of ventilation (air exchange) required to maintain the full genetic potential of poultry by providing sufficient oxygen and removing waste materials and gases resulting from growth and metabolism from the poultry rearing environment. This system should operate independently of any temperature control.
The challenge of minimum ventilation in cold weather depends on the poultry farm’s ventilation system, and ventilation requirements change based on the time of day, indoor and outdoor humidity levels, indoor and outdoor temperatures, wind speed, bird age, and stocking density. Due to constantly changing conditions, achieving the ideal minimum ventilation rate is difficult, and even more so for maintaining the entire flock. Minimum ventilation performs best when it operates with a thermostat and timer. Signs indicating proper minimum ventilation operation include:
- Oxygen supply proportional to the metabolic needs of the poultry.
- Relative humidity control.
- Maintaining suitable litter conditions.
Aviagen Company also outlines the following key points for using minimum ventilation:
- The minimum ventilation rate should be calculated at all times, not just by measuring outdoor air.
- Minimum ventilation is not suitable for high temperatures because it creates slow and gentle movement at the bird level. This is why minimum ventilation is suitable during brooding and for young chicks, or at night or in cool weather.
- Minimum ventilation should be controlled by a timer. Fans operate based on a time cycle, not temperature!
- Achieving proper negative pressure is crucial for ensuring incoming air is quickly drawn upwards towards the ceiling.
- The best way to determine the optimal minimum ventilation settings is to assess the behavior of the poultry and the poultry house environment.
To check the proper functioning of minimum ventilation, stand 2 to 3 meters away from the ventilation inlets. If you feel a draft of cold air during the timer’s operation, the inlets may not be adjusted correctly. Improper ventilation can have many consequences for poultry farmers. Therefore, correct adjustment and operation are very important. If you observe the following, you need to increase the number of minimum ventilation fans:
- RH (Relative Humidity) is abnormally high.
- Stuffiness in the air (stale air).
- High ammonia levels.
- Condensation and moisture are visible on water lines or poultry house walls.
- Wet litter.
On the other hand, you should decrease the number of minimum ventilation fans depending on the following:
- Very dry litter.
- Dust in the poultry house environment.
- The set temperature is not maintained consistently day and night (but air quality is acceptable).
If the distribution of poultry in the poultry house is uneven, the following may be the cause:
- Cold air drafts.
- Incorrect adjustment of air inlets.
- Failure of the poultry house heater.
If the set temperature is correct but the birds are clustered in one area, check the following:
- Check the temperature with a control sensor to ensure the set-point temperature is not too low.
- If you observe signs of heat in the birds, such as poultry heat stress, check the following:
- Control sensor readings.
- Ensure the set temperature is not too high.
- High relative humidity (RH).
There is a misconception that minimum ventilation is not needed during warm seasons and weather, and that the summer ventilation system (tunnel ventilation) can replace minimum ventilation in the building.
First Stage of Minimum Ventilation:
- In the first stage, fans operate without a thermostat and with a timer.
- The minimum ventilation fans used in the first stage must operate at a constant speed.
- The capacity of fans operating with a timer should be such that they exchange the entire air volume of the building every 8 minutes.
To determine the required number of ventilation fans for a poultry house, the following formula is used:
Number of Fans =Fan Capacity (cubic meters per minute)/Poultry House Volume (cubic meters)
To calculate Poultry House Volume:
Poultry House Volume (cubic meters) = Average Height (meters) * Width (meters) * Length (meters)
Calculating Poultry House Ventilation: Number of Fans in Minimum Ventilation
The minimum ventilation system must have sufficient capacity to operate throughout the life of the flock. Daily adjustments should be made based on air quality and humidity. The on-time and capacity of the fans used for cyclical ventilation gradually increase until all installed minimum ventilation fans are utilized. The calculations for the number of fans required for minimum ventilation in a standard poultry house with a tunnel ventilation system are as follows:
Poultry House Floor Area × Air Exchange Rate / Fan Working Capacity = Number of Fans Required
Poultry House Length × Poultry House Width = Poultry House Floor Area
In general, the characteristics of minimum ventilation and when to use it are as follows:
- Used during brooding and cold seasons or when the poultry house temperature is below the set point.
- Timer-based operation.
- Uniform inlet distribution.
- Inlet operation based on “negative pressure”.
- Introduction of fresh air from outside.
- Exhaust of stale air from inside the poultry house.
- Directing incoming cold air towards the ceiling ridge.
- Removal of excess moisture to control Relative Humidity (RH).
- Generation of adequate and necessary heat.
- Very low air movement at bird level.
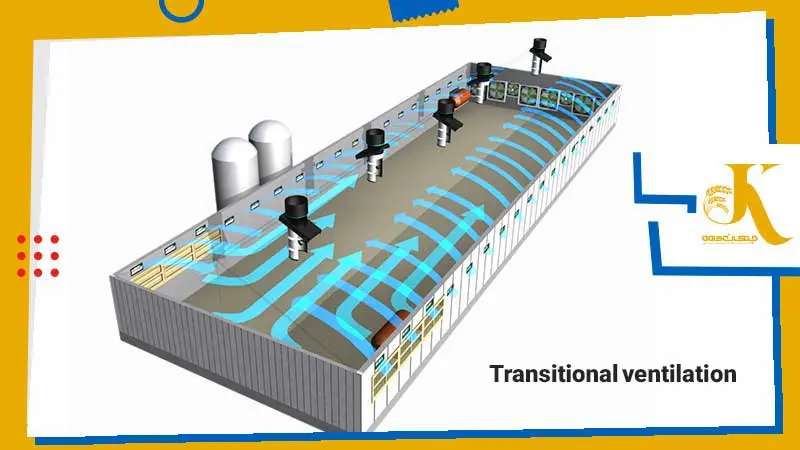
Transitional Ventilation
Transitional ventilation is used when the poultry house temperature is higher than the set point (by 1 to 2 degrees Celsius). The goal of transitional ventilation is to increase the air exchange rate with minimal air movement at bird level to maintain temperature, air quality, and heat removal. Ventilation inlets operate based on negative pressure. Incoming air should be directed upwards and away from the birds, as excessive airflow can disturb the chicks. Due to the large air volume during transitional ventilation, there will be some airflow and cooling effect on the poultry. Therefore, close attention to thermometers and sensors is necessary for making decisions based on bird behavior.
Observing Poultry Signs During Transitional Ventilation
If you observe signs of cold stress (such as clustering) while using transitional ventilation, take the following actions:
- Turn off one fan.
- Check inlet adjustments.
If you observe signs of heat stress in the birds (such as poultry heat stress), take the following actions:
If you are using the maximum capacity of transitional ventilation and it’s not effective, switch to tunnel ventilation for the poultry house.
In general, the characteristics of transitional ventilation and when to use it are as follows:
- Used when the house temperature rises above the set temperature, during cool weather, or when the birds are too young for tunnel ventilation.
- Temperature-based operation.
- Primary function is to remove excess heat.
- Introduction of a large volume of fresh air from outside.
- Inlet operation based on negative pressure.
- Directing air towards the ceiling peak.
Article: Specialized Poultry Farming Formulas examines the necessary formulas throughout the poultry production cycle
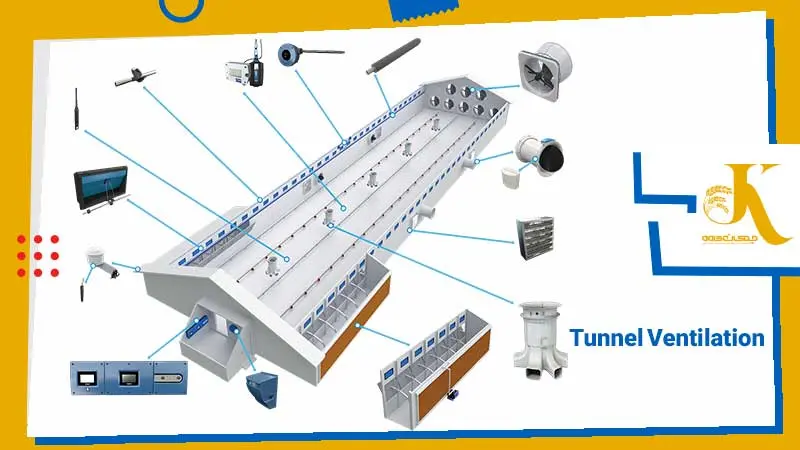
Poultry House Tunnel Ventilation: Tunnel Ventilation Fans in Rearing Buildings
Tunnel ventilation is a type of negative pressure exhaust system that involves installing exhaust fans (air exchangers) longitudinally in the rearing building for air ventilation. Tunnel ventilation systems are used to mitigate the negative effects of high temperatures during warm seasons (summer). In tunnel ventilation, all fans are located at one end of the building, and the inlets are at the other end. If the poultry house is very long (more than 300 feet or about 91.5 meters), you should consider tunnel ventilation for the building. This system helps air flow well throughout the entire length of the building, preventing heat from accumulating at the far end, where the exhaust fans expel the air, thus avoiding discomfort for the poultry.
The following method is used to calculate the number of tunnel ventilation fans:
Fan Capacity (cubic meters per second) / Required Fan Capacity (cubic meters per second) = Number of Tunnel Fans
Airflow Velocity × Poultry House Cross-sectional Area = Required Fan Capacity
Width (meters) × Height (meters) = Poultry House Cross-sectional Area (square meters)
Note: The most suitable fans for tunnel ventilation systems are high-capacity fans with a diameter of 1.2 meters and a capacity of 10 m³/s at the static pressure during operation.
Note: Due to regional differences in summer temperature and humidity, the desired airflow velocity also varies from region to region.
Procedure for Measuring Average Air Velocity in a Poultry House with Tunnel Ventilation
Air velocity can be measured at any time during the flock’s life, but ideally, it’s measured at least once a month (for broiler breeders) or once per cycle (for broilers). This is because air velocity is also considered part of a program to diagnose ventilation problems.
Measure the air velocity when the tunnel ventilation fans are operating. Ensure all sidewall inlets are closed.
- Air velocity measurements should be taken at a distance of 30 meters or 100 feet from the tunnel fans, at 3 or 4 locations across the width of the house. In a broiler poultry house, air velocity should also be measured above the inlets, as air movement is more restricted in these areas.
- Turn on the anemometer and ensure it is set to measure average air velocity.
- Hold the anemometer at arm’s length in front of you and away from any obstructions such as feeders or cages.
- Measure the air velocity in the poultry house using the anemometer.
- Wait for the reading to stabilize before noting the wind speed.
- Measure the air velocity at several points in the poultry house using the same method.
- The average air velocity is automatically calculated using the average speed setting on the anemometer. If your anemometer does not provide an average, you can obtain it yourself by noting the speeds and taking their average. The actual average air velocity recorded in the poultry house should be compared to the expected average air velocity along the length of the house. The method for calculating airflow velocity in the poultry house was provided in the tunnel ventilation fans section.
In general, the characteristics of tunnel ventilation and its applications are as follows:
- Tunnel ventilation is used during hot weather (or hot with high RH).
- Tunnel ventilation is used for older birds (with fully developed feathers).
- Tunnel ventilation is used when transitional ventilation is no longer able to keep the birds cool.
- High airflow velocity around the poultry.
- Creating wind chill for cooling poultry.
- Most importantly, a rapid air exchange rate.
One of the best indicators for determining which type of ventilation is needed is observing changes in bird behavior. Below, we examine factors along with solutions when using tunnel ventilation:
- • If you observe signs of cold stress in the birds, turn off some of the fans.
- If 50 to 60 percent or fewer of the tunnel ventilation fans are operating and you observe signs of cold stress in the birds, revert to transitional ventilation.
- If you observe signs of excessive heat in the poultry, turn on a tunnel fan.
- If all tunnel fans are on and the birds still feel cold, increase the cooling set-point temperature by 0.5-1.0 degrees Celsius.
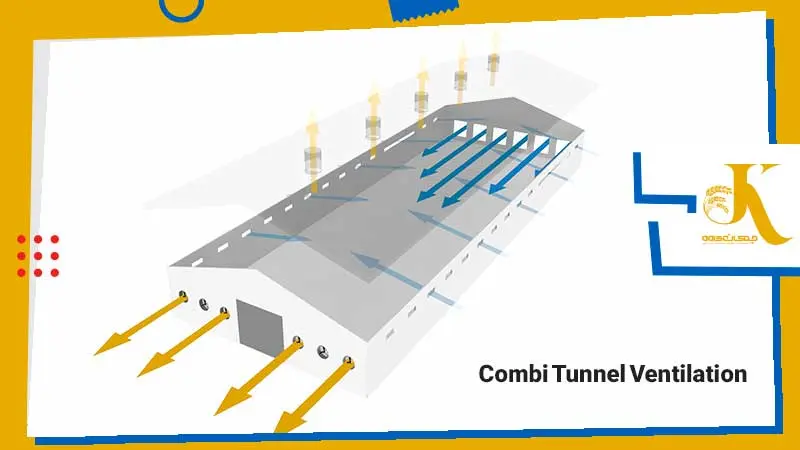
Combi Tunnel Ventilation
In combi tunnel ventilation, the tunnel ventilation airflow passes through the length of the poultry house or is directed to the middle of the building where roof ventilation fans are installed. When the fans are turned on, air enters through the evaporative cooling pads or duct windows and exits through the negative pressure exhaust fans and the roof fans. This method is the best ventilation approach during cold weather and the early stages of rearing.
How Many Fans are Needed for a Poultry House?
As you know, good and fresh air is very important for the well-being and growth of chickens. Just like stale air makes us humans feel uncomfortable, chickens also need proper poultry house ventilation to stay lively and grow.
Now, the question arises: how many fans should be in a poultry house to maintain balanced and good air quality?
To give a clear answer to this question, it must be said that there is no specific number. The number of fans depends on several factors, such as the size of the poultry house, the breeding season, and the age and weight of the chickens.
Considerations for Fan Height and Placement in Poultry Houses
The issue of fan installation height in poultry houses, despite frequent general searches, requires careful and specialized examination within the framework of ventilation system design. Determining the optimal fan height is influenced by numerous factors, including the dimensions and configuration of the building, the type of ventilation system (including cross ventilation, longitudinal ventilation, and tunnel ventilation), the climatic conditions of the region, and the technical specifications of the fans being used. Therefore, providing a fixed value as a standard height lacks technical validity and can lead to poor ventilation system performance.
In designing an efficient ventilation system, in addition to the installation height of exhaust fans from the floor, attention to the horizontal distance between fans, as well as the height and position of air inlets, is of great importance. The correct arrangement of the ventilation system components should ensure that fresh air is evenly distributed throughout the building space and prevents the creation of ventilation dead spots. Based on some common practices, the installation height of fans from the floor is usually considered to be in the range of 70 centimeters to 1 meter and 20 centimeters. However, it must be emphasized that this range is a general guideline and can vary depending on the specific conditions of each poultry house.
It is worth noting that the fans used in the poultry farming industry are produced in various sizes and airflow capacities, among the most common of which are 140×140 cm fans with an approximate airflow capacity of 44,000 cubic meters per hour and 100×100 cm fans with an airflow capacity of around 24,000 cubic meters per hour. Accordingly, determining the exact number and position of the required fans necessitates precise engineering calculations, considering the building volume and the required air exchange rate based on the age and stocking density of the poultry.
To achieve optimal ventilation system performance and ensure the health and production efficiency of the flock, it is recommended that employers consult with experienced specialists in the field of designing ventilation systems for poultry houses.
What is the Difference in Poultry House Ventilation Between Winter and Summer?
During cold seasons like winter, when the air is cool and cold, there is usually no reason to leave the doors open. In winter, the poultry farmer tries to keep the poultry house warm and the air fresh by managing the ventilation. For this reason, in winter, approximately 0.5 to 1 cubic feet per minute (CFM) of air is needed in the poultry house for every pound (about half a kilogram) of bird weight. This equates to about 0.014 to 0.028 cubic meters per minute.
But beware of the summer heat! During warm seasons, poultry farmers must pay close attention to air exchange to prevent the chickens from suffering from heat stress. In the summer season, 1.5 to 2 CFM of air is needed for the same pound of weight. This is about 0.042 to 0.057 cubic meters per minute, meaning approximately 2 to 3 times more air is required for the chickens in the summer.
Poultry House Air Purification: How Often Should the Air in a Poultry House Be Changed?
As a general rule for chicks younger than one month, it is best to change the air in the poultry house between 6 to 8 times per hour. For older and larger birds, this number increases to 10 to 12 times per hour. Following this guideline ensures that fresh air is always circulating in the poultry house. As a result, bad odors and airborne pollutants are minimized.
How is the Fan Arrangement System in a Poultry House?
A uniform airflow system in the poultry house is a very important matter. If this is not done correctly, one part of the poultry house will become too hot, and another part too cold. For this reason, the fans should be placed at a standard distance from each other to ensure that the air temperature is uniform throughout the building. Therefore, it is best to install the fans approximately every 25 to 30 feet (about 7.60 meters to 9.15 meters) on the side walls of the building. Under such conditions, the air throughout the rearing building will be uniform.
Key Points for Evaluating Ventilation in Poultry Houses
Ultimately, ventilation performance is crucial. This is because ventilation in poultry houses can act like a double-edged sword. Just as proper ventilation is very effective in improving performance, an improperly designed ventilation system itself causes serious damage to the poultry farmer. Therefore, checking the ventilation systems and their performance is very important. Below, we have listed important points in evaluating the ventilation of poultry farms:
- Evaluating the Building When Empty: When the poultry house is empty, evaluate the building for 20 to 30 minutes in terms of bird distribution, number of feeders, drinkers, and air quality. After making the necessary changes, check and note all items again after 20 to 30 minutes.
- Airflow and Obstruction Check: Pay attention to the placement of fans and air inlets in the poultry house environment. The presence of trees, walls, or any other obstacles near the exhaust outlets of the fans can act as windbreaks and significantly reduce the efficiency of the fans. This reduction in efficiency must be considered in the calculations for the number of fans required to ensure proper ventilation.
- Heater Check: Ensure that the heaters are installed at the appropriate height and are operating at maximum efficiency. Inspect and service the heaters before starting the building heating operation.
- Thermostats or robes Check:
- The thermostat should be installed at bird level in the middle of the house.
- A minimum-maximum thermometer should be installed next to the thermostat.
- Daily temperature changes should be recorded, and the temperature fluctuation should not exceed 2 degrees Celsius within a 24-hour period.
- Floor Temperature Check:
- Before chick placement in the building, it is necessary to heat it so that the floor temperature, building environment, and building humidity reach the desired level at least 24 hours before chick placement.
- To achieve the above goals, it is necessary to start heating the buildings at least 48 hours before chick placement.
- The duration of this heating varies between different farms depending on weather conditions, building insulation, and the heating capacity of the building.
- Before 5 days of age, chicks are unable to regulate their body temperature, and this ability is not fully developed until 14 days of age. Therefore, during this period, the litter temperature must be maintained at an appropriate level. If the litter and building air temperatures are too low, the internal body temperature of the chicks will drop, and they will huddle together. In these conditions, they consume less feed and water, resulting in lower growth rates and increased susceptibility to diseases.
- At the time of chick placement, the floor temperature should be 32 degrees Celsius if pressure heaters are used, and if brooder stoves with radiant heaters are used, the floor temperature at the heat source should be 40.5 degrees Celsius.
- Paying Attention to Poultry Behavior: Ventilation is used for the comfort of the birds and air quality. Therefore, bird behavior and air quality are the best ways to evaluate poultry house ventilation.
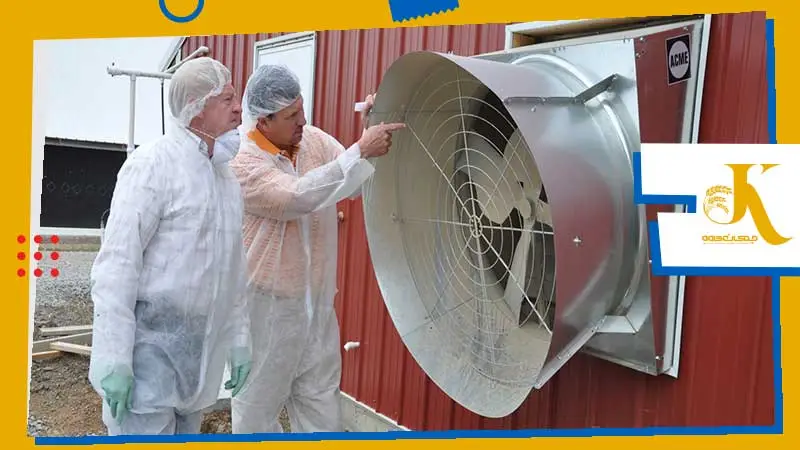
Poor Poultry House Ventilation Performance: The Reason for Chicks Clustering in One Area of the Building
As mentioned in the previous section, bird behavior is one of the helpful factors in evaluating poultry house ventilation. For example, how the chicks are distributed throughout the building can provide valuable information about ventilation quality and temperature uniformity. Specific patterns of clustering or avoiding certain areas often reflect existing problems in the ventilation system. In the following, we will point out some of the signs that indicate poor poultry house ventilation performance:
- Uneven Chick Distribution: Uneven bird distribution is due to non-uniform temperature in the poultry house.
• Chicks Clustering in the Middle of the Building: The reason chicks gather in the middle and avoid the sides is very low wind speed. - Reason for Chicks Clustering Along the Walls: Chicks standing, not moving, and not sleeping on the right and left sides of the building indicate a high wind speed in the poultry house.
- Chicks Getting Cold Due to High Wind Speed: The solution to this problem is to turn off some fans and open the inlet curtain openings of the cooling pad.
References: